Reformer beds have become increasingly popular in the realm of fitness and rehabilitation. These versatile pieces of equipment are designed to enhance strength, flexibility, and overall body awareness through controlled movements. However, for those new to the world of reformer beds, the array of options and features can be overwhelming. This article aims to demystify reformer beds, providing essential insights for beginners considering a purchase.
Understanding Reformer Beds
At its core, a reformer bed is a piece of Pilates equipment that utilises springs, pulleys, and a sliding carriage to facilitate a wide range of exercises. The design allows users to perform both strength and flexibility training, making it a valuable tool for individuals of all fitness levels.
What Makes Reformer Beds Unique?
Unlike traditional gym equipment, reformer beds offer a unique blend of resistance and support. The adjustable springs provide varying levels of resistance, allowing users to tailor their workouts to their specific needs. This adaptability makes reformer beds suitable for rehabilitation purposes, as well as for those seeking to enhance their fitness routines.
Moreover, the design of reformer beds encourages proper alignment and body mechanics. This focus on form helps prevent injuries and promotes effective movement patterns, making it an excellent choice for beginners who may be unfamiliar with more complex exercises. The ability to engage multiple muscle groups simultaneously also means that users can achieve a full-body workout in a shorter amount of time, which is particularly beneficial for those with busy schedules.
Key Components of a Reformer Bed
Understanding the components of a reformer bed is crucial for making an informed purchase. Key features include:
- Carriage: The sliding platform where the user performs exercises.
- Springs: Provide resistance and can be adjusted to suit different exercises and fitness levels.
- Pulleys and Straps: Allow for a variety of movements and positions, enhancing the versatility of the reformer.
- Footbar: Offers support and stability during exercises.
Each of these components plays a vital role in the functionality of the reformer bed, contributing to its effectiveness in delivering a comprehensive workout. Additionally, the reformer bed’s compact design makes it an ideal choice for home use, as it can often be stored away when not in use, saving valuable space. Many models also come with attachments or accessories that further expand the range of exercises available, allowing users to continually challenge themselves and keep their workouts fresh and engaging.
Furthermore, the reformer bed can be a social experience, as many studios offer group classes that foster a sense of community. Participants can motivate each other while learning from experienced instructors who can provide personalised guidance and adjustments. This social aspect not only enhances the enjoyment of exercising but also encourages accountability, making it easier for individuals to stick to their fitness goals.
Benefits of Using a Reformer Bed
Reformer beds offer a multitude of benefits, making them an attractive option for both beginners and experienced practitioners alike. Understanding these advantages can help individuals make a more informed decision when considering a purchase.
Enhanced Strength and Flexibility
One of the primary benefits of using a reformer bed is its ability to improve both strength and flexibility. The resistance provided by the springs allows users to engage various muscle groups effectively. This engagement not only builds strength but also enhances flexibility, as many exercises require a full range of motion.
Regular use of a reformer bed can lead to noticeable improvements in muscle tone and overall physical fitness. This is particularly beneficial for individuals looking to complement their existing fitness routines or those recovering from injuries.
Improved Posture and Alignment
Another significant advantage of reformer beds is their focus on posture and alignment. The design encourages users to maintain proper body mechanics throughout their workouts. This emphasis on form can lead to better posture in daily life, reducing the risk of musculoskeletal issues.
For those who spend long hours sitting at a desk or engaging in repetitive movements, incorporating reformer exercises can help counteract the negative effects of poor posture. Over time, users may find themselves standing taller and moving more freely.
Choosing the Right Reformer Bed
When it comes to purchasing a reformer bed, there are several factors to consider. Not all reformers are created equal, and understanding the differences can help buyers make an informed choice that suits their needs.
Types of Reformer Beds
Reformer beds come in various styles, each designed for specific purposes. The most common types include:
- Standard Reformers: These are versatile and suitable for a wide range of exercises, making them ideal for beginners.
- Compact Reformers: Designed for home use, these models are often more lightweight and easier to store.
- Studio Reformers: Built for commercial use, these are typically more robust and feature additional adjustments and accessories.
Choosing the right type depends on the intended use, available space, and budget. Beginners may find standard reformers to be the most suitable option as they offer a comprehensive introduction to Pilates exercises.
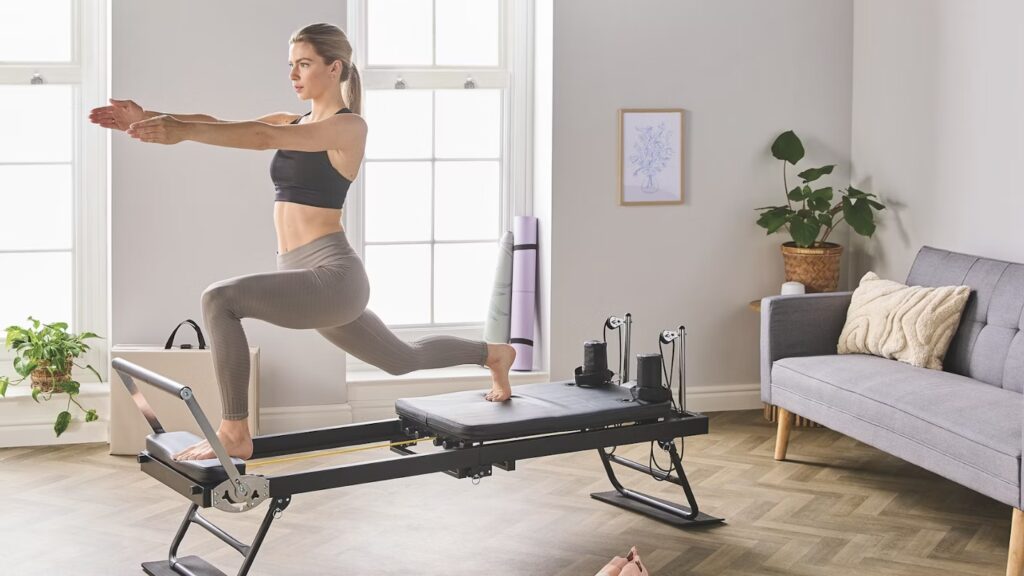
Budget Considerations
Reformer beds can vary significantly in price, from budget-friendly options to high-end models. It is essential to establish a budget before beginning the search. While it may be tempting to opt for the cheapest option, investing in a quality reformer can make a substantial difference in the long run.
Higher-priced models often come with better materials, more adjustable features, and improved durability. Additionally, consider the warranty and customer support offered by the manufacturer, as these factors can contribute to the overall value of the purchase.
Essential Accessories for Your Reformer Bed
While a reformer bed can be used effectively on its own, several accessories can enhance the experience and expand the range of exercises available.
Common Accessories
- Footstraps: These provide additional support and can be used for various exercises.
- Jump Boards: Allow for cardio workouts and plyometric exercises.
- Extra Springs: For those who want to increase resistance options.
Investing in a few essential accessories can help users maximise their workouts and keep their routines fresh and engaging.
Finding the Right Space
Before purchasing a reformer bed, it is crucial to consider the space available for use. Reformer beds require a certain amount of room to operate effectively, especially when performing exercises that involve movement. Ensure that there is enough space not only for the reformer itself but also for the user to move freely.
Additionally, consider the flooring. A stable, non-slip surface is ideal for performing exercises safely. If using the reformer in a home environment, it may be beneficial to designate a specific area for workouts to encourage consistency and routine.
Getting Started with Your Reformer Bed
Once a reformer bed has been purchased, the next step is to begin using it effectively. For beginners, starting with a structured approach can help build confidence and ensure proper technique.
Consider Professional Instruction
While many exercises can be learned through online resources and videos, seeking professional instruction can be invaluable, particularly for beginners. A qualified Pilates instructor can provide personalised guidance, ensuring that movements are performed correctly and safely.
Many studios offer introductory classes specifically designed for beginners, which can provide a solid foundation for future workouts. This investment in professional instruction can lead to better results and a more enjoyable experience.
Establishing a Routine
Consistency is key when it comes to making progress with a reformer bed. Establishing a regular workout routine can help users stay motivated and committed to their fitness goals. Aim to incorporate reformer workouts into the weekly schedule, gradually increasing the intensity and complexity of exercises as confidence and strength grow.
Tracking progress can also be beneficial. Keeping a journal of workouts, noting improvements in strength, flexibility, and overall well-being can provide motivation and a sense of achievement.
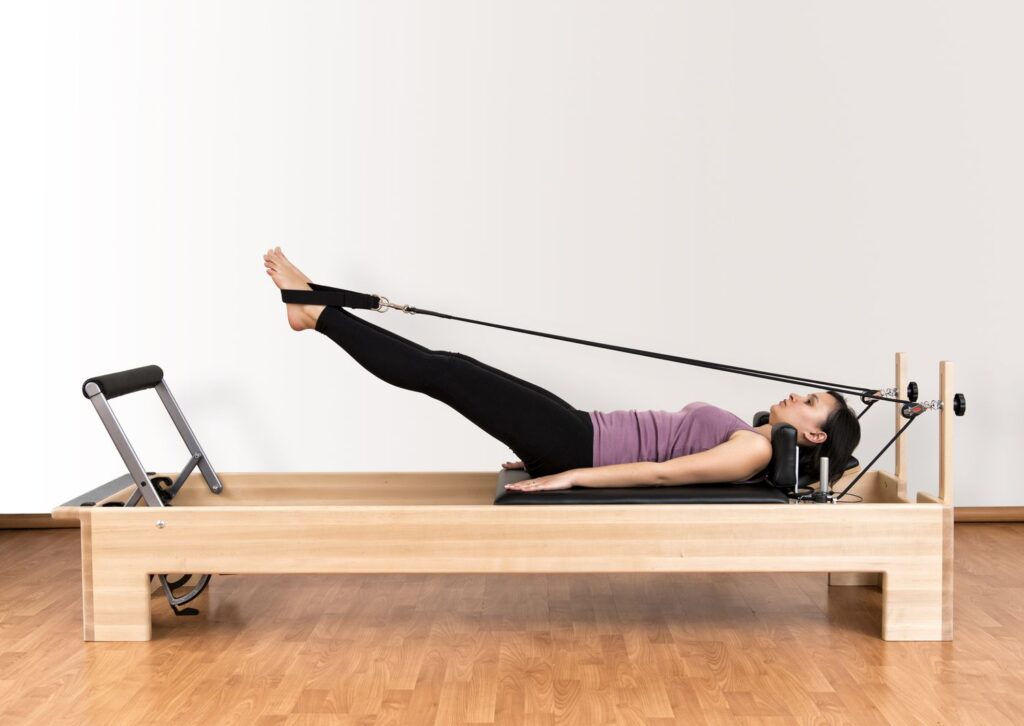
Conclusion
Reformer beds offer an exciting and effective way to enhance fitness, improve flexibility, and promote overall well-being. For beginners, understanding the fundamentals of reformer beds, their benefits, and how to choose the right model is essential for a successful start. With the right approach, incorporating a reformer bed into a fitness routine can lead to significant improvements in strength, posture, and overall health.
By investing in quality equipment, considering professional guidance, and establishing a consistent routine, individuals can unlock the full potential of reformer beds and enjoy a rewarding fitness journey.
See Also: Are Foldable Reformers worth it? pros and cons for home pilates.